Safety Toolkits
Build a Strong Safety System with SafetyPack
SafetyPack is what the name says – a single health and safety management package that gives you affordable resources for building and maintaining your health and safety system.
There are four service types:
- Concise Service – polishing up what you already have.
- Compact Service – all the above with fully detailed implementation instructions.
- Collaboration Service – all the above with facilitated meetings to ensure you confidently achieve the end result.
- Comprehensive Service – all the above with a customisable cloud-based safety management system SafetyBase. It comes with an initial four hours complimentary customising of your choice!
What is the process?
-
Building a Safety System Building or repairing a Safety System is like building or repairing a house. Start at the foundations and work up. Details are last.
- For all our Services below, the current health of your Safety Management System is assessed against the standard you want. The minimum legal standard in New Zealand is compliance with the Health & Safety at Work Act 2015.
- There are also ACC and Worksafe frameworks, proprietary systems and international standards including ISO45001.
- Our experienced safety expert completes an assessment against the standard you require and how you manage your risks.
- Gaps and remedies will be reported against that agreed standard.
- Our Services range from providing a simple gap report, to detailed recommendations, usable tools, and mentoring.
If you don’t have a Safety Management System, or need to improve your Safety Management System, we have SafetyBase, a world class cloud-based system with three
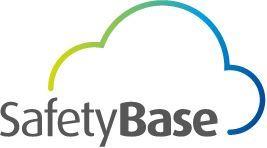
distinct editions and price points. It’s included in the Comprehensive Service (see below), but it can be added to all the options. You can choose any of the four Services (see below) or you can mix and match. Just decide which combination you think is best for your business and get in touch.
Helping organisations to jump health & safety hurdles is our core business. To discuss options and ask questions, call +64 0800 000 267 or email info@safetypro.co.nz.
Name of SafetyPack Service | What you receive | Price for 1 – 50 employees | Price for 50-100 employees Click here for more employees |
Comment |
Concise Service |
|
$600 – $960 | $960 – $1540 | Choose this if you just need a tune-up and access to expert help. |
Compact Service |
|
$1080 – $1730 | $1080 – $2770 | As above, plus detailed recommendations and prioritised action plan |
Collaboration Service |
|
$1800 – $2880
|
$2880 – $4610
|
As above plus mentoring, problem solving and guidance at monthly video meetings.
|
Comprehensive Service |
|
Set Up fee $2250. Thereafter, |
Setup fee $2250 to $4500. Thereafter $751 to $1500 per month software licence
|
Have your own custom data entry forms with SafetyBase Enterprise Edition. Example, your in-house checklists online and mobile |
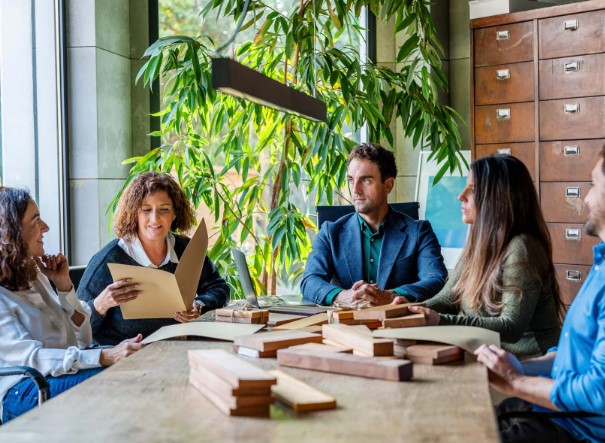
*For all Services above, a choice of three Safetybase editions can be added.
Example 1. A manufacturing company is required to use a corporate safety management system. Then they find out that an internal audit is coming up in 6 months.
They have the manual and forms and an internal OHS Advisor. So they just want to know where the gaps are, get some support and have it all done before the audit.
The “Concise” Service of SafetyPack really hits the spot. Their Safety Advisor doesn’t have to create a system because she already has the corporate one. The SafetyPack gap report and four months of included assistance is all she needs.
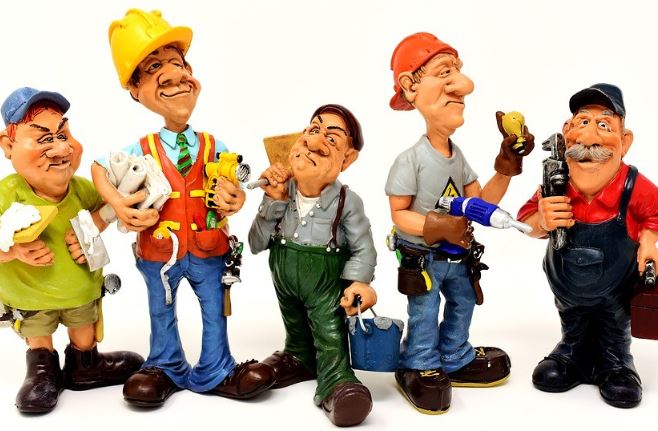
Example 2. A small construction company with 10 employees and up to 30 contractors is inspected by Worksafe. The company has no safety management system and Worksafe issues them with an Improvement Notice: Four months to get it done!
They go for the “Compact” Service in SafetyPack, which provides detailed recommendations within a step-by-step Implementation Plan.
They see an opportunity in having a ready-made Safety Management System so they also ask for the Professional Edition of SafetyBase. Why? Because apart from having all the essential features, it allows them to design and automate contractor agreements and inductions.
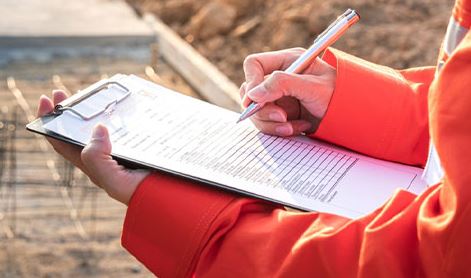
Example 3. An accommodation and food service business is an Accredited Employer in the ACC’s incentive scheme. They need an independent expert to run the ruler over their safety management requirements after an acquisition.
The SafetyPack expert knows the ACC requirements and writes detailed recommendations and a step-by-step Implementation Plan. The company likes the idea of video meetings in the “Collaboration” option. It ensures the implementation goes without a hitch.

Example 4. A nationwide retailer that also has two distribution centres has committed to getting ISO45001 certification. They have been using a paper-based system, which makes it difficult to have the same approach across all sites.
In view of their ambitious plan to conform with a high standard, the organisation wanted the fully featured “Comprehensive” option, which includes the customisable SafetyBase Enterprise edition.
This was essential to future-proof their data gathering formats. For example, they use a large number of checklists, for racking, company vehicles, forklifts and safety inspections. Some long-standing forms also need to be replicated in the software.
An end-to-end solution!
Simon Lawrence, Director, SafetyPro Limited
In at the Deep End
It’s not much fun finding yourself under pressure with your safety. For some reason, you are facing scrutiny. It may be after an inspection by authorities. Perhaps a corporate initiative to comply with a standard. Just as accounting systems are audited, safety systems do too. It only takes a few months for shortcuts and ad hoc actions to creep in.
You don’t have the time to do all the preparation, and even if you did, it’s going to take you ten times longer. You’ll need to acquire a whole new layer of knowledge. You have no problem doing the implementation, but a bit of structured safety advice would be very helpful.
It’s not just audits that test your resources. There are other similar circumstances. Here are the four most frequent. They are scenarios regularly encountered by health and safety advisors. And they are all problems that can be resolved simply and efficiently.
Most frequent issues:
- Worksafe has inspected you or investigated an incident. They may have: required improvements by a specified date; threatened or actually issued an Infringement Notice; worst of all, they may be considering prosecution. What you do next is critically important.
- A big client has once more requested that you send them your “Safety Plan”. Before contract renewal. That means “This time we really mean it”. It’s the way things are done these days. But you need to know what game is being played. You need to play it too, but you can do it with integrity.
- Head Office wants a safety audit and your “system” is full of holes. In fact, that big dusty manual has gone missing too. Not the end of the world. First of all, the thicker a manual is, the less practical use it is. Secondly, we will get you going with simple, meaningful stuff. In fact, you are probably already doing some useful things. Before you know it, you are ready for audit.
- Your safety person moved on and nobody really knew what they used to do. Then, someone found out that unfortunately, the safety person didn’t know what they were doing either. So they had been winging it for a few years. Time to get back to basics. Together, we straighten out the big things first, then the rest falls back into place.
- There’s a new manager who says you need to implement a Safety Management System. And you agree. Of course! Now what? Big dark tunnel. But we have headlights and a vehicle to get you to the other end. And the experience to remove obstacles.
The good news is, all of these situations are far simpler than they appear. And you are perfectly capable of doing the things you need to do. But you just need to know what those things are, in which order to do them, and to be able to navigate past the inevitable obstacles. For example, you have no idea how to assess (say) a chemical hazard and how to decide what control measures are needed; or safety meetings spend a whole hour talking about why things can’t be done. Because analysing is more fun than actually doing something.
It’s at times like these an experienced outsider can make a big difference.
So here’s a typical list of the sort of steps involved:
- We find out what YOU want as the end result. (This sounds obvious, but we do prefer to avoid “stock” solutions).
- We identify the obstacles and time-frames you have. Also, what you are currently doing/have not been doing.
- We identify a broad approach and timing that everybody can live with.
- Once that’s done, you will get a simple documented Implementation Plan that’s prioritised, with basic building blocks first and details last. Like building a house.
- You assemble a small internal Implementation Team that will meet at an agreed frequency to work through the Plan in bite-sized pieces. The Team will include our help to keep focused and solve problems as they arise. Although we don’t chair meetings, we can use a reset button if things bog down.
- We provide “hands-on” horsepower if appropriate. For example, if you are implementing a safety management system, it’s often useful for us to assist in getting the Hazard/Risk Register developed. And if that means walking around and looking at stuff, we can do that, to get you started.
- Unlimited email and telephone support for the duration of the project.
- It’s a good idea to finish off with a quick confirmation check, just to make sure it’s all hanging together.
If you would like a chat, call 0800 000 267
Safety Planning and Review
This is the stuff you do AFTER you have put your safety management system in place. Because it’s what avoids the manual getting dusty or the safety person wandering off-grid.
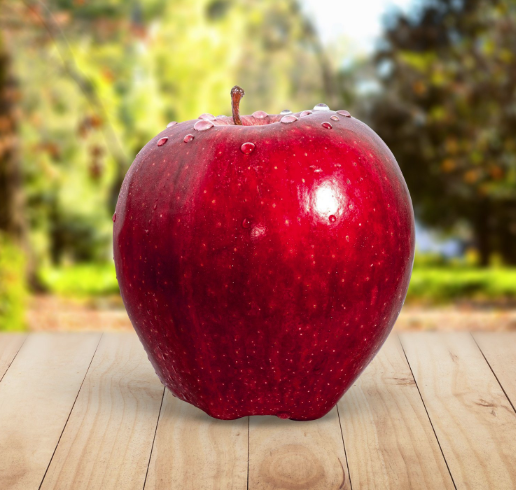
Systems need to be kept fresh and healthy by a process of continuous review and improvement. This means some type of awareness and monitoring is needed, preferably continuous rather than once in a while. Here are some frequently used methods:
- Invest in regular training of managers and key employees in what safety is all about. Make sure they understand what the word risk actually means, and how it guides us in day-to-day safety.
- Set reasonable objectives for improvement. To be successful, it’s best to make them simple and practical. Easier to have agreement about small, tangible achievements than to try and change the world right now.
- Get the skills to face the heat and find honest insights about the deeper causes of accidents and near misses. Don’t ignore the benefits of unpeeling the onion to find underlying causes. It’s easy to blame but it’s not productive.
- Mostly, we are not naturally competent in accident investigation. There are simple techniques available. Training key people is essential.
- Review hazard controls at least annually and after significant changes in processes. New technology is now constantly offering solutions that didn’t exist until recently.
- Think about your communication with workers. You don’t have to be “woke” to accommodate communication styles for cultural, gender and social reasons.
- Look at ways to involve workers not just in “consultation” (informing and getting feedback from workers), but also the more active “participation” (workers co-developing inside the safety system).
- Think outside the square with emergency preparedness. For example, toolbox meetings and safety meetings could routinely have short conversations about scenarios such as medical events or specific injuries.
- Review the health of the safety system annually, using a checklist broadly based on the above. External experts may lack local knowledge but are perhaps more likely to apply a fresh approach and provide creative safety advice. There is, however, a role for both internal and external audits.
Either way, the system itself needs life breathed into it all the time.
If you would like a chat, call 0800 000 267
Supervisors and Managers OHS Skills Courses
Health and safety should be a result of “doing things right” – and therefore part of the general drive for quality – getting things right first time. However, like any system, health and safety has some unique processes to follow. So specific knowledge of these processes makes “doing it right” a lot easier.
For example:
- A supervisor ought to know what a Notifiable Event is because those events must be reported to Worksafe.
- At the general level, managers are more able to make safe decisions if they understand the meaning of risk. And its relationship with what is “reasonably practicable” under the law.
- Knowing how to conduct an insightful accident investigation is a skill that does not come naturally to most people.
Why train supervisors and managers?
Senior leaders want a safety system to work. So line managers and supervisors must understand how to support that. And senior leaders themselves must receive safety advice or they will get it wrong too.
Our training courses are always a process of “opening windows of understanding”. And you don’t get that from just watching a PowerPoint show. There has to be something else as well. Sure, visual displays are used but we also have discussions together. That is how we answer all the questions. Because key facts are understood better when there is active participation.
And you get answers to all your questions.
Here are my most popular training topics. All of them are half a day or less.
Understanding the Health and Safety at Work Act.
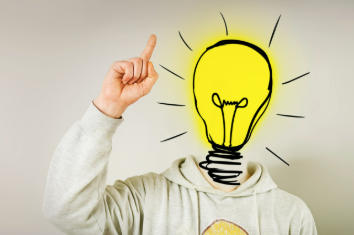
On the face of it, this has to be a dry subject, doesn’t it? But unless managers and key workers have a grasp of what the Act actually does require, the world will remain full of myths and misunderstandings.
And there are plenty of myths about health and safety. But how do we make this topic genuinely interesting? Well, the training highlights all the key aspects of the Act. The “aha” moments are discovered using open ended questions. It works because together, we find the answers to all those questions. So here are just four examples:
- “A fork lift stops suddenly and a pallet, being carried 2 metres above floor level slides off. No one is hurt. Is this incident reportable to Worksafe?”
- “What is a valid reason for a worker to refuse to do a job for health and safety concerns?”
- “Can anyone agree a contract to exclude, limit or modify the operation of the Act?”
- “If I’m an employee health and safety rep, will I be prosecuted if there’s something unsafe?”
This is a half-day course for 2 to 20 people. Cost is either a flat fee of $750 plus GST or $200 plus GST per person, whichever is the lesser cost.
Hazard Management (And Taking a Risk).
This topic is central to an employer’s duties under the Act. Because work has hazards. Just day-to-day living has hazards. It’s not bad to have hazards. For example, when you drive home after work, you are busy managing hazards by constantly assessing risks, taking preventive actions and hopefully following rules like stopping at red lights.
Workers do not have to be “wrapped in cotton wool”. In fact, an employer’s duty is to do what is reasonable for the risk. So understanding reasonable risk is the core purpose of this training. And That’s what gives rise to my sub-heading “(And Taking a Risk).” In other words, we have to talk about risk and work with it.
This is a half-day course for 2 to 20 people. Cost is either a flat fee of $750 plus GST or $200 plus GST per person, whichever is the lesser cost.
Accident Reporting and Investigation
Strangely enough, the current Act says nothing directly about internal recording of accidents, nor the need to investigate them. The previous Act was very clear about it. Never mind, we have to work with what we’ve been given.
This training course clarifies statutory requirements for reporting Notifiable Events. Also for internal recording of incidents. So having clarified accident reporting and recording, we examine accident investigation in detail. Because it’s an opportunity for improvement. However, for many people, it’s not a skill that comes naturally.
We kick off by finding out how good the group already is at investigating. We look at the three main reasons we should investigate incidents, and we learn a simple but effective investigation technique. Finally, we return to the initial investigation to see if we improved. Which we always do.
This is a half-day course for 2 to 20 people. Cost is either a flat fee of $750 plus GST or $200 plus GST per person, whichever is the lesser cost.
Examples of other available training
- Contractor Management.
- Machine Guarding
- Conducting Safety Inspections
- Isolation of Machinery
- Preventing Manual Handling Injuries
- Preventing Gradual Process Disease
- Effective Safety Committees
- Understanding and Managing Stress
If you would like a chat, call 0800 000 267